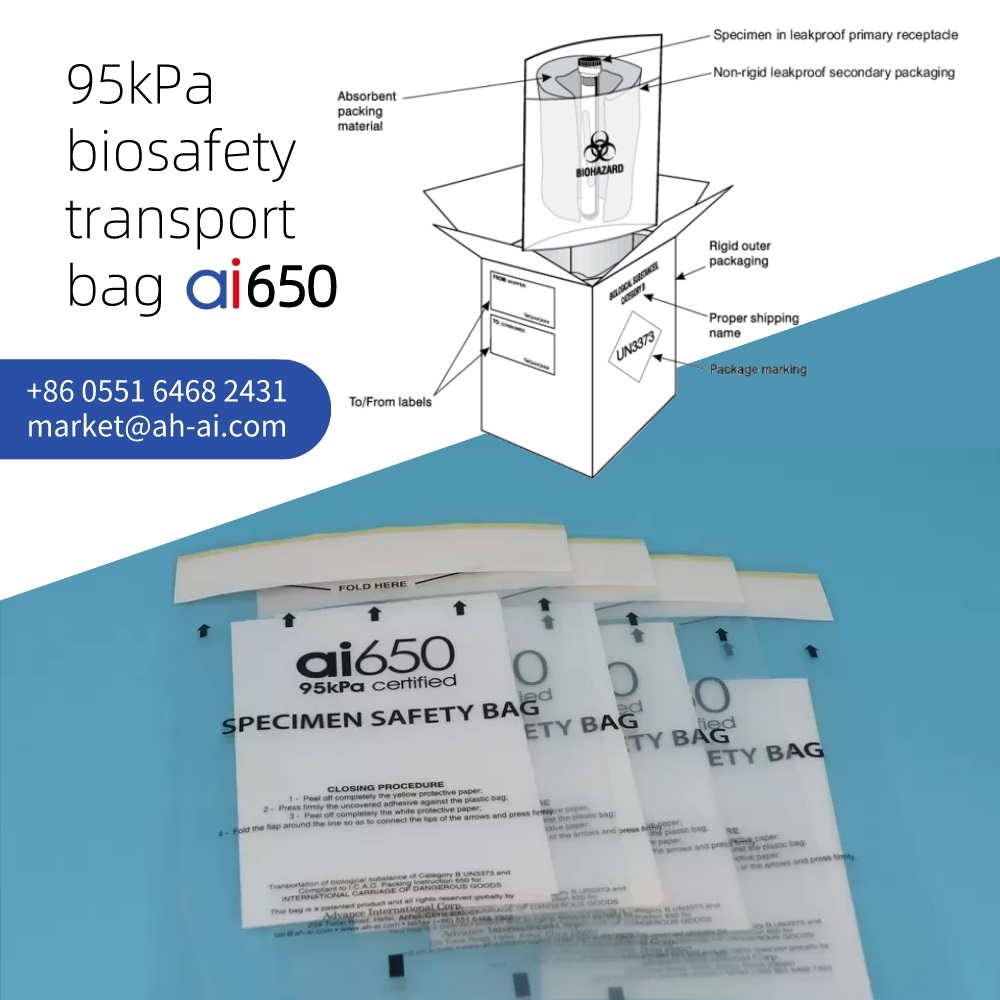
Originally published in Clinical Laboratory Today–Ensuring specimen
The financial cost of diagnostic errors is extremely high for the U.S. health care system. According to the Centers for Disease Control and Prevention (CDC), approximately 14 billion laboratory tests are ordered each year. And an estimated $750 billion is wasted on unnecessary services and according to the American Academy of Pediatrics publication Hospital Pediatrics. On the low efficiency. Some of these errors may be diagnostic errors due to– improper technique, identification errors, labeling errors, improper storage and shipping conditions, quality issues, etc. These can lead to delayed treatment, misdiagnosis and, in the worst cases, harm to the patient.
The cost of trust these errors impose on patients and their families is unquantifiable. Patients may be misdiagnosed due to labeling errors, or critical treatment may be delayed due to missing tissue biopsies. Stories of such serious incidents make the news every year and are often the only time diagnostic errors receive national attention.
Medical Errors: A Leading Cause in America
However, recent estimates suggest that diagnostic errors affect more than 12 million people in the United States each year and may result in approximately 64,000 preventable deaths each year. While not every diagnostic error will have life-changing consequences, every error has the potential to cause harm. With so much at stake, how can hospitals and healthcare organizations reduce errors to support effective patient care?
To help ensure that patients receive the best possible care, specimen integrity (necessary conditions required to prevent specimen damage) must be established, protected, and improved. Doing so requires everyone involved in the diagnostic workflow to focus on reducing errors. This requires a comprehensive approach to maintaining appropriate processes, products, systems and especially a safety culture.
Reduce variability and human error
Laboratory testing is supported by technical staff. Without medical laboratory professionals, nurses, clinicians, phlebotomists and other healthcare professionals collecting, transporting and testing specimens, many test results would not be available. Therefore, some degree of human error is unavoidable and, therefore, there is a need to enhance sample integrity using products, systems, and processes that reduce or eliminate human error from the equation.
Sample integrity initiatives extend beyond organizations. For example, the Clinical Laboratory Standards Institute (CLSI) recently established a new target of 1% blood culture contamination as part of best practices. With the current benchmark set at <3%, this new standard represents a significant reduction in errors and potential savings for facilities that can limit contamination rates to 1%.
Products specifically designed to reduce pollution can help in this regard. Standardized collection kits can also improve sample integrity by minimizing variability during sample collection, transportation, and processing.
How distributors can improve sample integrity
The responsibility for sample integrity falls on everyone in healthcare, including manufacturers, suppliers, and distributors of diagnostic products. Specifically, healthcare distributors are positioned to facilitate collaboration between clinical and supply chain teams. Distributors have a unique and advantage as intermediaries between manufacturers and medical institutions
allowing them to identify pitfalls and roadblocks in the sample collection workflow.
Resellers can help advance healthcare organizations’ specimen integrity programs by standardizing and sourcing high-quality specimen collection and transport products that are specifically designed to maintain specimen integrity throughout the workflow and reduce fragmentation to strengthen the supply chain. Collaboration to ensure sample integrity is more important than ever—because patients have high expectations.
You can learn more about AIC resources to improve sample integrity here.