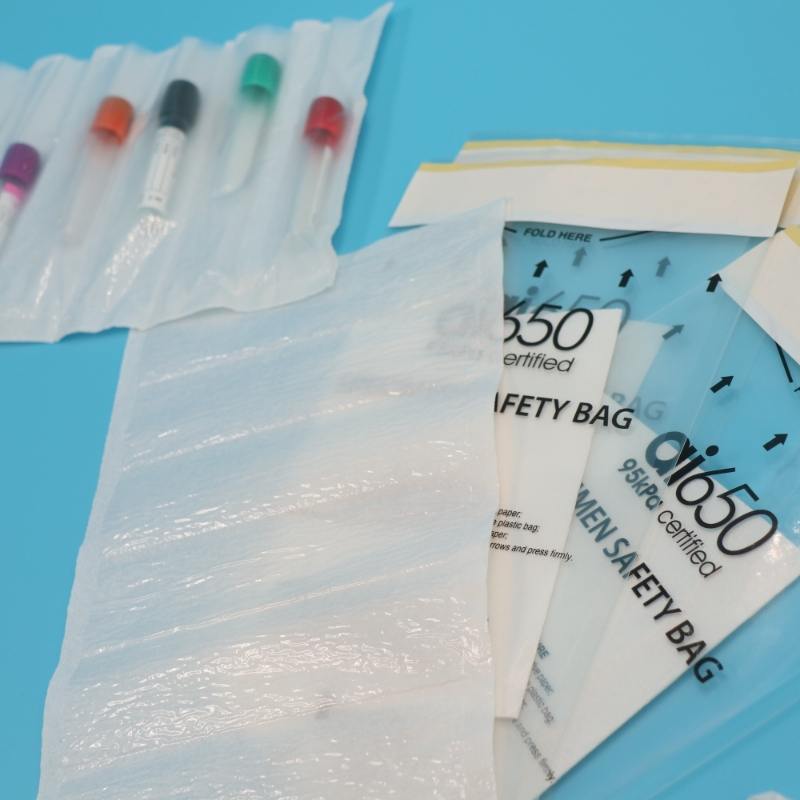
n various industries, the need to maintain an airtight seal is paramount to ensure product integrity, freshness, and safety. This is particularly true when dealing with modified atmosphere packaging (MAP) where specific gas compositions are used to extend shelf life or preserve quality. Sealing a bag at 95kPa (kilopascals), which corresponds to approximately 0.94 atmospheres, requires precision and adherence to best practices. Here’s a comprehensive guide on how to achieve this effectively:
Understanding the Importance of 95kPa Sealing
Before delving into the process, it’s crucial to grasp why sealing at 95kPa matters. This pressure level allows for the removal of oxygen and replacement with inert gases like nitrogen or carbon dioxide, creating an environment that inhibits aerobic bacteria growth, slows down oxidation processes, and helps retain product color, flavor, and texture. It’s widely used in food packaging, pharmaceuticals, and electronics sectors.
Preparation Phase
- Select Suitable Materials: Choose high-quality barrier films designed for your application. These should have low gas permeability to maintain the desired atmosphere within the package. Common materials include ethylene vinyl alcohol (EVOH) copolymers, polyester, and polypropylene layers.
- Equipment Check: Ensure your vacuum sealer or packaging machine is calibrated correctly to achieve and sustain the 95kPa pressure. Regular maintenance and servicing are vital for consistent performance.
- Product Preparation: For solid products, ensure they are dry and free from excess moisture. Liquids should be filled carefully to avoid spillage during sealing. If necessary, use inserts or trays to stabilize items inside the bag.
Sealing Process
- Insert Product & Gas Flush (if applicable): Place the product into the bag, leaving enough headspace as required by your packaging design. If using gas flushing, introduce the desired gas mix slowly into the bag before sealing, ensuring even distribution without causing product disturbance.
- Vacuum Creation: Initiate the vacuum process, gradually reducing the internal pressure to remove air. Most machines allow adjusting the vacuum level; set it to reach around 95kPa below atmospheric pressure. Monitor the pressure gauge closely to confirm accuracy.
- Heat Sealing: Once the target pressure is achieved, proceed with heat sealing. The temperature and dwell time will depend on the bag material and thickness but typically range between 180°C to 220°C for a few seconds. Ensure even heating across the seal area to create a strong bond without damaging the contents.
- Cool Down & Final Check: Allow the sealed bags to cool naturally or use a cooling mechanism if available. After cooling, visually inspect each seal for completeness and perform random leak tests using methods such as vacuum decay or helium leak detection to verify the integrity of the seal.
Post-Sealing Considerations
- Labeling & Coding: Clearly label each package with essential information including production date, batch number, and any special handling instructions. Consider using smart packaging technologies like QR codes for traceability.
- Storage Conditions: Store the sealed packages in a cool, dry place away from direct sunlight to maximize their shelf life. Adhere to any specific storage requirements related to the product type and gas mixture used.
- Quality Assurance: Implement a robust quality control program that includes periodic checks on sealed bags’ integrity throughout their shelf life. This helps identify potential issues early and ensures ongoing compliance with industry standards.
By following these steps meticulously, you can successfully seal bags at 95kPa, safeguarding the quality and longevity of your products while meeting regulatory and consumer expectations. Remember, attention to detail at every stage—from material selection to post-sealing inspections—is key to achieving optimal results.